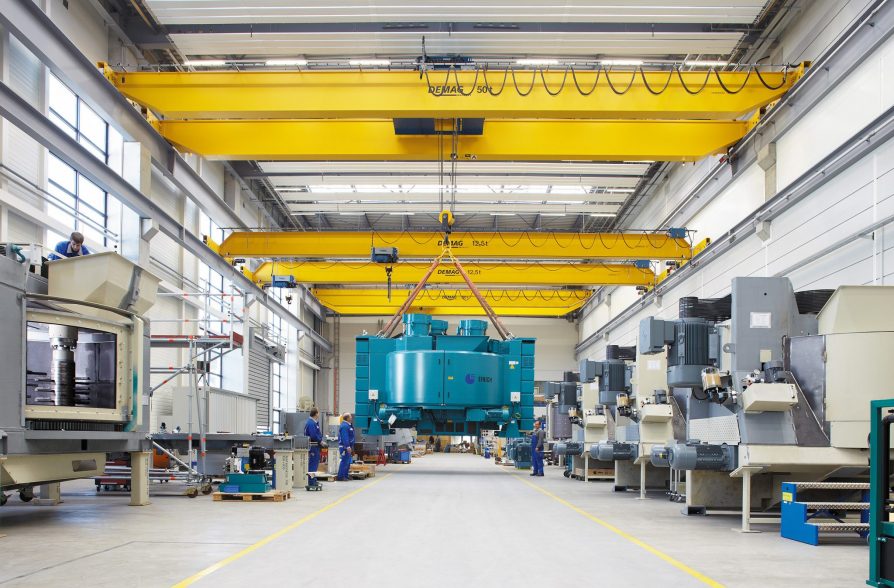)
An Integrated Crane System from Demag for German Engineering Firm
The Gustav Eirich mechanical engineering plant in Hardheim, Germany, has fitted out a new production bay with Demag cranes.
On two levels, an integrated intralogistics solution has been installed that can be used for both transporting large and heavy mixers, as well as for serving the assembly stations with components.
Additionally, a two-crane-level concept has been adopted in the neighbouring paint shop operated by the company, which specialises in industrial processing systems. The two-level concept makes it possible to achieve flexible workplace design. Thanks to the compact configuration of the Demag cranes and hoist units, the height of the workshop is utilised to its full potential. This has enabled investment, maintenance and energy costs to be reduced in the long term.
The integrated solution, which consists of seven Demag crane installations, is based on a masterplan for reorganisation of the production processes.
Uwe Greissing, factory manager at Eirich and responsible for implementation of the new production strategy, said: “As a mechanical engineering company, we need reliable partners who provide us with advice throughout all phases and help us to select the appropriate technologies.”
Two 12.5t Demag EKKE single-girder overhead travelling cranes were installed in the assembly area, where they travel at a height of 9.6m and serve the assembly stations with the required sub-assemblies and electric motors. On the level above, two Demag ZKKE double-girder overhead travelling cranes, which each have a load capacity of 50t, operate at a height of 12.5m.
This solution now enables Eirich to handle fully assembled large mixers weighing up to 46t safely as a complete unit. The DR 20 hoist units feature two-stage operation. This ensures that loads can be transported quickly and that the heavy machinery can be positioned precisely and carefully. To meet rising demand in the future, both cranes have been designed for tandem operation, which enables the total weight that can be transported to be doubled to almost 100t.
All cranes in the assembly bay can be controlled independently of each other via radio control. If large components have to be moved or turned, the cranes on the upper and lower levels approach each other to within a defined minimum distance. Thanks to the special arrangement of the rope drums in the cross-travel direction on the upper crane level, the distance between the hooks can be reduced.
Work in the neighbouring paint shop is supported by two ZKKE overhead travelling cranes, which have load capacities of 50t and a span of 9.85m. A 12.5t single-girder overhead travelling crane operates on the runway installed below.
As in the assembly bay, the cranes that operate above the painting stations are equipped with frequency inverters for smooth starting and variable travel speeds in the cross-travel direction.
All Demag cranes are fitted with processor-based controls, which satisfy in full the safety-relevant functions as required by the Machinery Directive.